High Life Steel Shots
If components are blasted with High Life Steel Shots to produce the surface finish, production economy plays a significant role in particular, apart from the positive optical effects. If the component hardness is 40 HRC or less then here low-hardness High Life Steel Shots is the first choice. High longevity due to higher Manganese% and low plant wear and tear are the outstanding properties of this abrasive.
These abrasives are resistant to impact, which is absorbed homogeneously on the whole shot surface. Lower the hardness more is the longevity. Unlike high-carbon abrasives, no surface cracks are observed and thus a considerably higher longevity is achieved at minimum wear of the plant components. When produced, High Life steel shot has 43-44 HRC initial hardness and this level reaches up to 49-50 HRC during the use due to manganese as well as contribution of other elements which is maintained until shot becomes unusable.
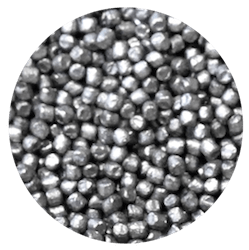
Features of Our High Life Steel Shots
Its cylindrical round shape helps to clean faster. The rate of cleaning will be ultimately increased by at least 25% of your Blasting Machine.
Where you will require 6 kgs for shot blasting of 1-ton material, by using High Life Steel Shots you will just require 3 kg.
Equal hardness and size and excellent homogeneity.
After few hours of usage, during the shot blasting process, the High Life Steel Shots become fully rounded due to its natural tendency.
Due to fine grain size, shots lives for days and weeks, until every shot reduces to micro particle; they do not break into dust.
Components blasted with High Life Steel Shots have much greater life than the same components blasted with any Normal Shots/Grits, because it maintain there blasting intensity longer than any other shot type.
Shot used in the shot blasting process should be at least as hard as the part being blasted (+-5 HRC)
Being used in more cycles (2-4 times), High Life Steel Shots reduces the cost for maintenance and warehouse.
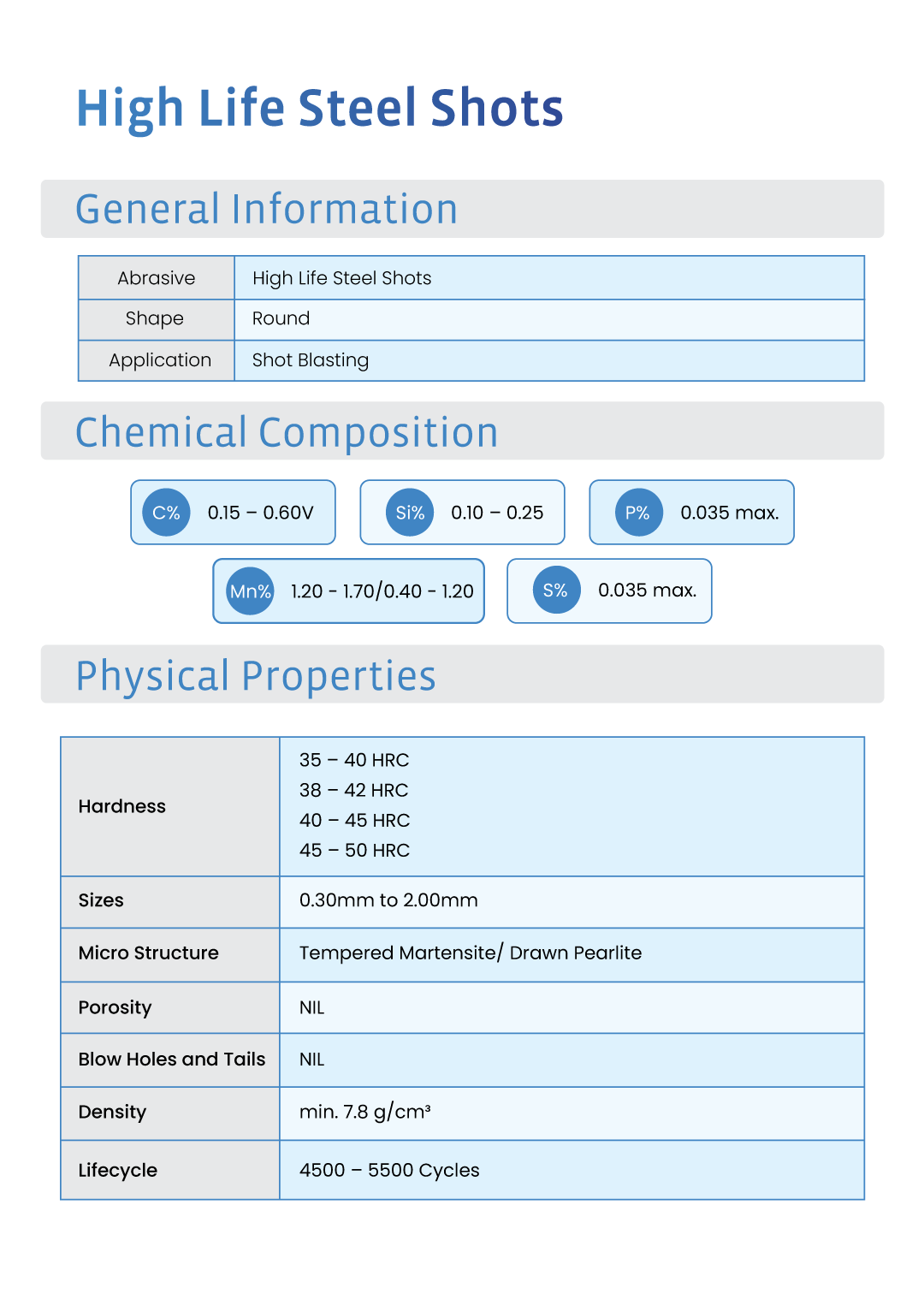
Applications
Sand Removal, De-burring, Descaling, Oxide Removal, Surface Treatment, Stress Relieving and other various types of applications.
